Mastering Light Weight Aluminum Casting: a Deep Study the Numerous Techniques Available
Aluminum casting stands as a keystone of modern-day manufacturing processes, supplying convenience and accuracy in creating practical components and detailed styles. As industries increasingly transform to aluminum for its light-weight yet long lasting residential or commercial properties, mastering the numerous spreading methods ends up being paramount. From the typical technique of sand spreading to the complicated processes of financial investment casting and pass away spreading, each method presents special challenges and benefits. Recognizing the nuances of these approaches is vital for guaranteeing the top quality and efficiency of the spreading process. In this expedition of light weight aluminum casting methods, we will clarify the complexities of each approach, giving understandings that can transform your strategy to aluminum casting.
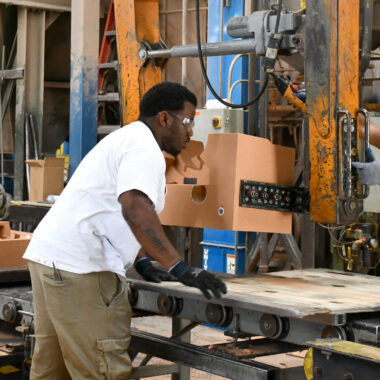
Sand Casting Technique Overview
The Sand Spreading method's flexibility and widespread application make it a keystone in mastering light weight aluminum casting procedures. This method entails developing a mold and mildew from a mix of sand and a binder, such as clay, to create complex forms for casting molten aluminum. Sand spreading is a popular selection as a result of its reasonably low price, simplicity of modification, and capability to produce intricate geometries with high precision.
The procedure begins with the creation of a pattern, usually made of wood or steel, which is pressed into the sand to develop a mold dental caries. When the pattern is gotten rid of, the mold and mildew cavity is full of molten light weight aluminum, which solidifies to take the form of the pattern. After cooling and solidification, the sand mold is escaped, revealing the light weight aluminum spreading.
Sand casting is commonly made use of in various markets, consisting of automobile, aerospace, and production, due to its versatility in generating both big and little aluminum components (aluminum casting). Its adaptability to detailed designs and cost-effectiveness make it a favored selection for many light weight aluminum spreading applications
Permanent Mold Spreading Refine Discussed
Exploring the ins and outs of light weight aluminum spreading, the Permanent Mold Casting procedure offers a refined technique for developing premium parts with precision and efficiency. Unlike sand casting, long-term mold casting uses a multiple-use mold and mildew typically made from steel or iron to shape the liquified aluminum. The mold is preheated to a specific temperature to enhance the flowability of the metal before pouring. This process assists accomplish a smoother surface area finish and tighter resistances compared to sand casting.
Irreversible mold and mildew casting can be categorized right into 2 primary types: gravity casting and low-pressure casting. Gravity spreading entails pouring the molten metal into the mold making use of gravity, while low-pressure casting utilizes low pressure to fill the mold and mildew tooth cavity. Both methods offer benefits in regards to minimizing porosity and enhancing mechanical residential properties.
Pass Away Casting: Benefits and Downsides
Grasping the intricacies of die spreading includes understanding its distinctive advantages and drawbacks in the realm of light weight aluminum component manufacturing. Die casting offers a number of benefits that make it a prominent selection for creating light weight aluminum parts. One vital advantage is the high-speed manufacturing capability of die spreading, permitting for the mass manufacturing of intricate shapes with limited tolerances. Additionally, pass away casting provides exceptional dimensional accuracy and smooth surface coatings, lowering the need for extra machining processes. The process is likewise extremely repeatable, ensuring constant top quality across big manufacturing runs.
However, die casting does include its very own set of drawbacks. One significant downside is the high first tooling cost related to developing the passes away made use of at the same time (aluminum casting). These molds can be pricey to generate, making pass away casting much less affordable for small manufacturing runs. The process is not as versatile when it comes to create modifications contrasted to other casting techniques like sand casting. In spite of these restrictions, the advantages of die casting typically exceed the disadvantages, making it a preferred selection for several light weight aluminum spreading applications.
Financial Investment Casting Benefits and applications
Structure on the advantages of die casting, investment read casting supplies a flexible approach for generating intricate aluminum elements with special benefits in numerous applications. Financial investment casting, additionally called lost-wax casting, masters producing complex forms that would be challenging or difficult to attain with other approaches. This technique is extensively used in markets such as aerospace, vehicle, and jewelry production.
One of the crucial benefits of financial investment casting is its capacity to produce near-net form parts, decreasing the requirement for additional machining and decreasing product waste. This results in price savings and faster manufacturing times compared to standard machining procedures. Additionally, investment spreading allows for the production of get rid of excellent surface coatings and tight resistances.
In the Discover More Here aerospace sector, investment casting is preferred for its ability to create light-weight yet solid parts essential for aircraft efficiency. The auto field take advantage of investment spreading for generating components with high dimensional accuracy and detailed styles. Generally, financial investment spreading offers a accurate and cost-efficient solution for manufacturing intricate light weight aluminum components throughout numerous sectors.

Lost Foam Casting: Just How It Functions
Lost foam spreading, likewise referred to as evaporative-pattern spreading, is a technique for creating complex metal components by utilizing foam patterns that vaporize throughout the casting procedure. This method starts with a foam pattern of the wanted part being positioned into unbonded sand. The foam pattern is generally covered with a refractory product to boost the surface area finish of the last metal component. When liquified metal is put right into the mold, the visite site foam evaporates due to the warm, leaving a dental caries that is then loaded by the metal.
Among the essential benefits of lost foam casting is its capability to generate intricate shapes with complex information that might be challenging to accomplish with various other casting methods. Furthermore, the procedure can be cost-efficient as it eliminates the requirement for cores and permits the combination of several parts right into a solitary part. It needs mindful control of the process specifications to make sure appropriate foam vaporization and metal circulation.
Verdict
In verdict, understanding light weight aluminum casting includes understanding and using various techniques such as sand spreading, irreversible mold and mildew spreading, die casting, financial investment spreading, and lost foam casting. Each technique has its very own benefits and applications in the manufacturing procedure. By familiarizing oneself with these different approaches, makers can select the most ideal spreading technique for their details demands and requirements, ultimately resulting in effective and successful production of light weight aluminum elements.
From the traditional approach of sand spreading to the facility processes of investment spreading and die spreading, each technique presents special difficulties and benefits. In this exploration of aluminum spreading methods, we will certainly shed light on the details of each technique, providing understandings that might revolutionize your technique to aluminum casting.
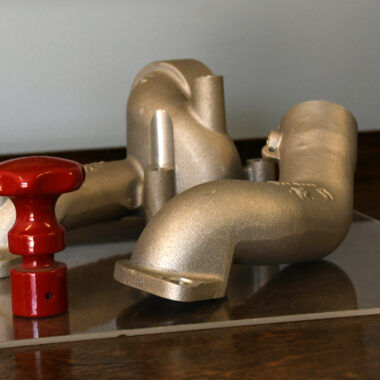